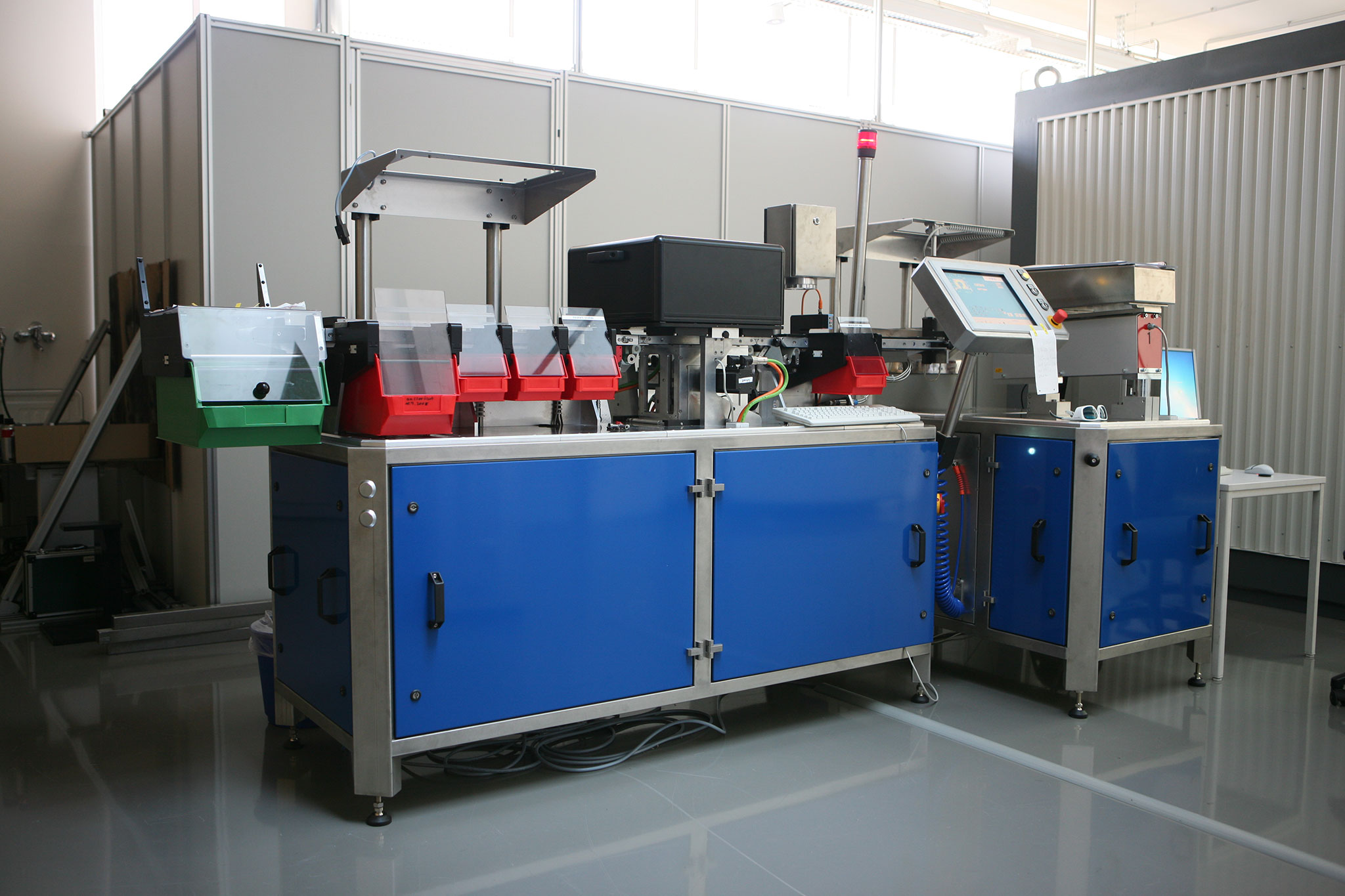
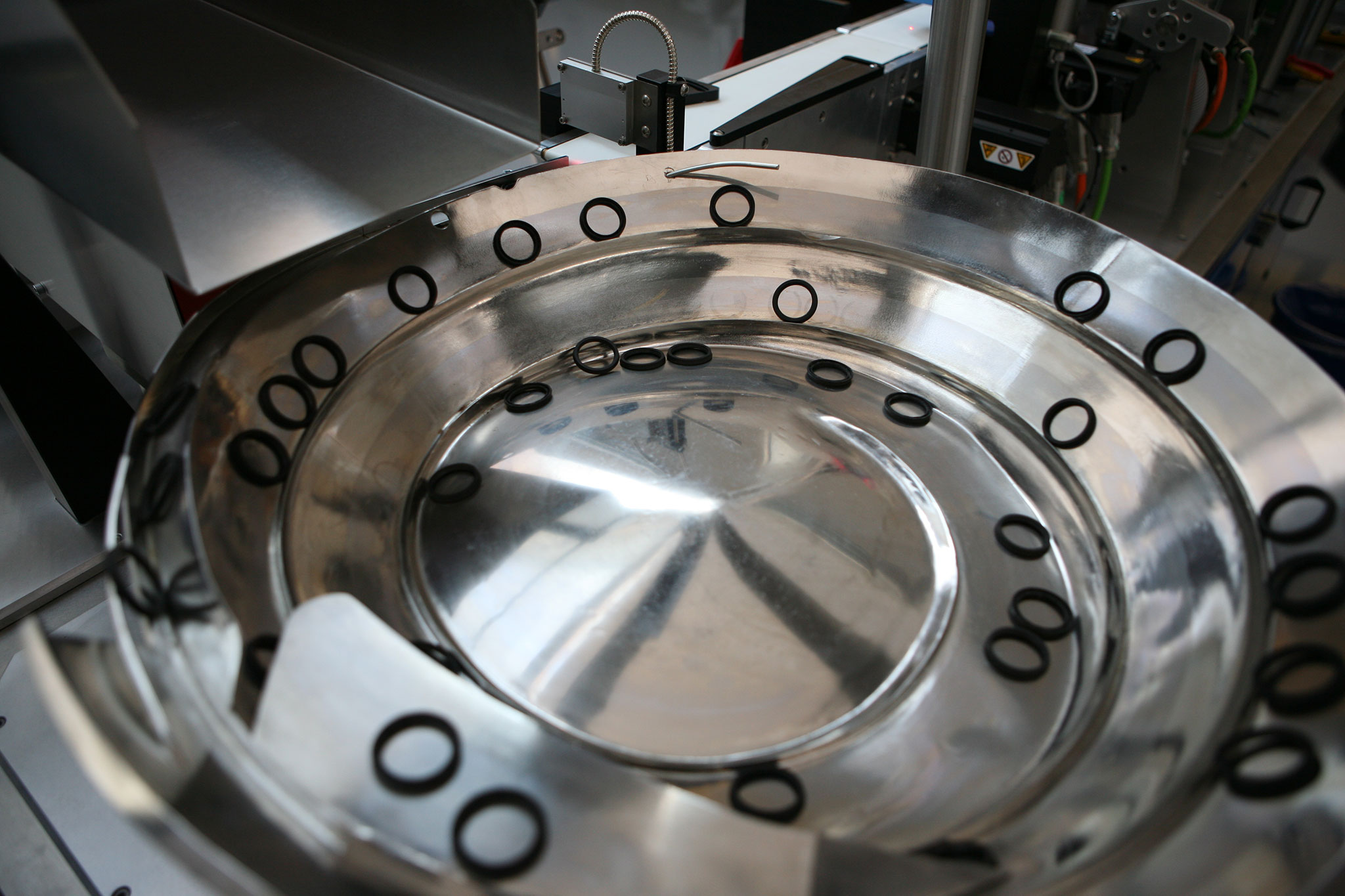
Polymer sealing rings play an important role in many areas of our lives, above all in vehicles. Typically, they are manufactured in an injection-molding or die-casting process. Because the material is injected into the mold from several injection points, if one of them is clogged, the material from the adjacent injection points must flow into this section of the mold. This creates a risk that a defect could occur which might be difficult to detect. Inhomogeneities in the material can also lead to problems in its use. Up to now, complex sealing rings have only been tested in manual inspections. Arguments against manual inspection are, for example, complex handling, enormous inspection quantities and long inspection times. The most efficient solution for inspecting mass-produced items is without question a fully automated testing system that is customized for the inspection task. This is the only way to assure quality in a reliable manner while taking economic aspects into consideration. SealInspector, a new, fully automated testing system, helps detect errors and provides an alternative to manual testing, which is complex and unsafe.
The system was developed in close cooperation between Fraunhofer EZRT and a system provider. The system components are arranged along a central conveyor where the sealing rings are transported. First, a vibration conveyor separates the rings, as bulk material, and places them onto a belt conveyor so that the same side is always facing up. Then the surface of the sealing rings is scanned and recorded from all sides. After the data collected in this manner is analyzed, potentially defective sealing rings are removed from the production flow with compressed air and collected in containers for a possible follow-up inspection. The sealing rings that pass all of the inspections are collected in a container at the end of the belt conveyor.