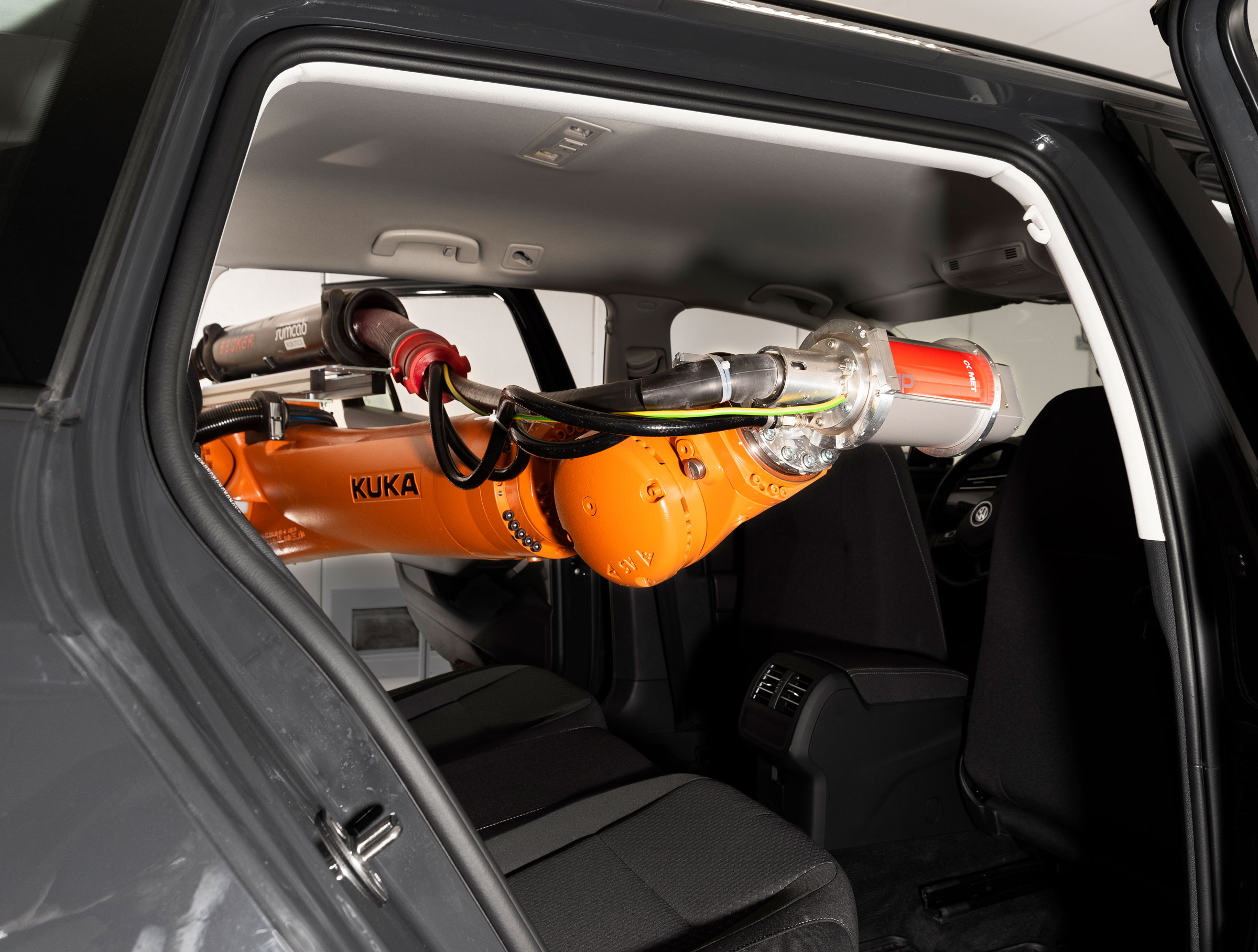
Each year, auto makers tear apart hundreds of brand-new car bodies using crowbars to check the workmanship of welded and bonded joints, bolts, and rivets. Holub hopes to supplant this time-consuming procedure with a smart X-ray technique called RoboCT, in which a CT scan is performed by synchronously operating movable robotic arms.
In industrial computed tomography, the X-ray source and detector are usually fixed, while the object to be examined is slowly rotated on a plate. During this process, X-ray images are captured from different angles and subsequently used to generate a 3D model. This static setup allows resolutions in the range of a few micrometers. Performing X-ray scans of larger objects such as cars requires very big and extremely expensive systems.